- Messages
- 13,385
- Reaction score
- 13,502
- Points
- 857
- Location
- Royal, AR
- Boat Make
- Yamaha
- Year
- 2007
- Boat Model
- SX
- Boat Length
- 23
Many Yamaha Boat models use this same horn.
Mine made a sound that my kids described as a pterodactyl crying. The replacement sounds more like a duck quacking and is significantly louder.
This is the replacement part which I found on Amazon for $35 Aqua Signal Dual Tone Electronic Hidden Horn (White). It is the newer 844017 model that is supposed to have a Gore-tex seal to keep it dry. The old and the new both had stickers on them that said "Waterproof". The original was part number 84422-1.
I removed the two screws that held the factory horn in place. The screws provided with the replacement are smaller so you will want to reuse the factory screws. Then I disconnected the wiring at the crimp connectors. The wiring harness wires are short so please be careful to avoid them falling back into the boat.
I removed the metal cover from the factory horn and reused it with this new one.
The next step of soldering and shrink tubing is unnecessary but it is my preferred way of making low voltage connections so I thought I would share. It also preserved the original wire length. As an alternative you could simply crimp new connectors onto the new horns shorter wires.
I cut the wires from the old horn at a length that once added to the new horn would be the same length as the original assembly. I had them side by side when I made this cut. Then I slid a small piece of shrink tubing over each wire and a third over both wires together. I moved the shrink tubing as far away as possible from where I would be soldering. Then I twisted the wires together and applied the iron and solder. I kept the iron on the wire until the wire sucked the solder in creating a solid bond.
I am using a Portasol 011289250 which is a 75 watt adjustable gas powered soldering iron. I have a couple of electric soldering irons both large and small but I really like the convenience of this little gas powered iron. It also has torch tips which I will use with the shrink tubing.
Then I pulled the shrink tubing over the solder joints and carefully switched to a torch tip.
I carefully shrank the tubing on each joint keeping the flame back from the wires and shrink tubing. I have a heat gun but this is a quick easy way to do it.
I like to apply an additional layer of shrink tubing over the combined wires. This layer is longer and adds strength and protection to the joints.
Now that I have an assembly that matches what the factory used I installed the factory metal cover and ran the factory screws through the horn and its gasket. The new gasket includes adhesive. I removed the backing paper from the gasket and used the screws to keep it in place as I installed the horn. I removed the horn and took this picture of the gasket attached to the hull.
This is a picture of the horn installed.
I looked for an alternative horn since I have heard of so many failures. I did not find anything that would fit in the same spot. So I plan to see how long a new horn lasts. Even if I have to replace it every year it is a $35 and less than 10 minutes job.
Mine made a sound that my kids described as a pterodactyl crying. The replacement sounds more like a duck quacking and is significantly louder.
This is the replacement part which I found on Amazon for $35 Aqua Signal Dual Tone Electronic Hidden Horn (White). It is the newer 844017 model that is supposed to have a Gore-tex seal to keep it dry. The old and the new both had stickers on them that said "Waterproof". The original was part number 84422-1.
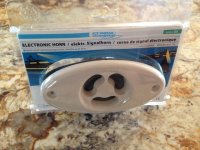
I removed the two screws that held the factory horn in place. The screws provided with the replacement are smaller so you will want to reuse the factory screws. Then I disconnected the wiring at the crimp connectors. The wiring harness wires are short so please be careful to avoid them falling back into the boat.
I removed the metal cover from the factory horn and reused it with this new one.
The next step of soldering and shrink tubing is unnecessary but it is my preferred way of making low voltage connections so I thought I would share. It also preserved the original wire length. As an alternative you could simply crimp new connectors onto the new horns shorter wires.
I cut the wires from the old horn at a length that once added to the new horn would be the same length as the original assembly. I had them side by side when I made this cut. Then I slid a small piece of shrink tubing over each wire and a third over both wires together. I moved the shrink tubing as far away as possible from where I would be soldering. Then I twisted the wires together and applied the iron and solder. I kept the iron on the wire until the wire sucked the solder in creating a solid bond.
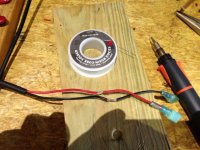
I am using a Portasol 011289250 which is a 75 watt adjustable gas powered soldering iron. I have a couple of electric soldering irons both large and small but I really like the convenience of this little gas powered iron. It also has torch tips which I will use with the shrink tubing.
Then I pulled the shrink tubing over the solder joints and carefully switched to a torch tip.
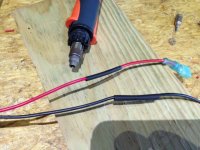
I carefully shrank the tubing on each joint keeping the flame back from the wires and shrink tubing. I have a heat gun but this is a quick easy way to do it.
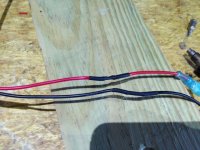
I like to apply an additional layer of shrink tubing over the combined wires. This layer is longer and adds strength and protection to the joints.
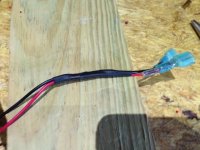
Now that I have an assembly that matches what the factory used I installed the factory metal cover and ran the factory screws through the horn and its gasket. The new gasket includes adhesive. I removed the backing paper from the gasket and used the screws to keep it in place as I installed the horn. I removed the horn and took this picture of the gasket attached to the hull.
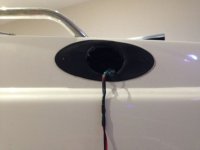
This is a picture of the horn installed.
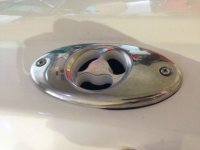
I looked for an alternative horn since I have heard of so many failures. I did not find anything that would fit in the same spot. So I plan to see how long a new horn lasts. Even if I have to replace it every year it is a $35 and less than 10 minutes job.