Speedling
Jetboaters Admiral
- Messages
- 5,158
- Reaction score
- 4,371
- Points
- 432
- Location
- Cedar Lake, IN
- Boat Make
- Yamaha
- Year
- 2008
- Boat Model
- SS
- Boat Length
- 21
My ladder was beat up.
It was used and abused over the years and would swing all the way in to the point where it would hit the boat when trying to get up. This was because the thin metal poles of the ladder kinked in mainly and also because it just wasn't properly spaced out.
What I did was simple yet effective. I got some stainless tubing and cut it to about 2 inches, and welded it around the stock pipes. Then, get 2 1/2 bolts (stainless) and re-use the washers and lock nut and the ladder sits properly now, and actually angles away from the boat making it even better than I had anticipated!
The extra thickness did require me to loosen the bolts holding the bracket that holds the ladder out when extended, or up when retracted, in order to drop them to the lowest possible point and allow the extra thick tubing to get through.
Just one of the little things I've done, so I figured I'd share since I know my ladder was pretty annoying to me.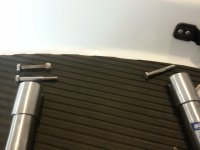
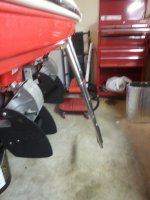
PS. Sorry second photo is a little out of focus. Camera phones ain't perfect man.
It was used and abused over the years and would swing all the way in to the point where it would hit the boat when trying to get up. This was because the thin metal poles of the ladder kinked in mainly and also because it just wasn't properly spaced out.
What I did was simple yet effective. I got some stainless tubing and cut it to about 2 inches, and welded it around the stock pipes. Then, get 2 1/2 bolts (stainless) and re-use the washers and lock nut and the ladder sits properly now, and actually angles away from the boat making it even better than I had anticipated!
The extra thickness did require me to loosen the bolts holding the bracket that holds the ladder out when extended, or up when retracted, in order to drop them to the lowest possible point and allow the extra thick tubing to get through.
Just one of the little things I've done, so I figured I'd share since I know my ladder was pretty annoying to me.
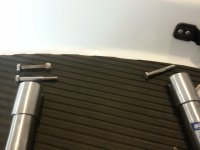
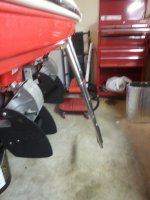
PS. Sorry second photo is a little out of focus. Camera phones ain't perfect man.